Stepper Motor Driver 3D Printer Step Stick MKS TMC2100
Stepper Motor Driver 3D Printer Step Stick MKS TMC2100 - The TMC2100 provides an integrated motor driver solution for 3D-Printing, Cameras, Scanners and other automated equipment applications. The device has an integrated microstepping indexer, the completely noiseless current control mode StealthChop™ and is intended to drive a bipolar stepper motor. The output driver block consists of low RDSon N-Channel power MOSFETs configured as full H-bridges to drive the motor windings. The TMC2100 is capable of driving up to 2.5A of current from each output (with proper heatsinking). TMC2100 is designed for a supply voltage of 5~46V. The device has a step and direction interface and can be configured with digital pins.
What if the stepper motor gets hot?
True, stepper motors can get warm. Their containers may reach temperatures of 100 to 110 C. This is due to the drive continuously providing the motor with full current in order to maintain the motor's position. (This is distinct from servos, in which the drive merely supplies the servo motor with the current necessary to keep it in place.) For this function, the servo has feedback while the stepper does not.)
Depending on how much electricity the drive is configured to pump into the motor, a stepper motor operating on a desktop without a heatsink runs the risk of burning out.
There are numerous methods for lowering the maximum temperature that a stepper motor can reach.
Attach a suitable heatsink to the motor. It makes a major difference to what the motor mounts to. A gearbox is not an effective heatsink. Likewise, a mounting plate that matches the motor's mounting flange in size does not work. When a stepper motor is on and off of a heatsink, the temperature difference can reach 40 degrees Celsius.
What is a good heat sink?
23 frame: 6-inch x 6-inch x .5-inch, 10-inch x 10-inch x 0.25-inch aluminiumheatsink
If the drive has a reduction capability, use it. The amount of current provided to some stepper drives is reduced when the motor is at a standstill thanks to some type of current reduction capability. Without the need of outside forces, this operates on horizontal loads. When this function is used, applied loads that are constantly attempting to reverse the motor could fall vertically with ball screws, belts, or low friction systems.
The system friction and loads determine whether a step motor would back drive in a current fold back state since step motors have more torque at low speeds and less torque is needed to hold a load than to accelerate a load. Lead screws are superior options because they are frequently self-locking or have a brake on a ball screw.
Ensure that there is adequate airflow. A stepper motor won't be able to dissipate heat in a small, constrained area. The motor's buildup of heat can be dissipated by using a fan and excellent airflow.
QUICK
- Hardware compatible with StepStick and Pololu A4988
- Drive capability up to 1.2A continuous coil current
- Step/Dir interface with microstep interpolation (up to 256 microsteps)
- Motor voltage: 5~46V
- Logic voltage: 5V (5v version)
- stealthChop - for quiet operation and smooth motion
- spreadCycle - highly dynamic motor control chopper
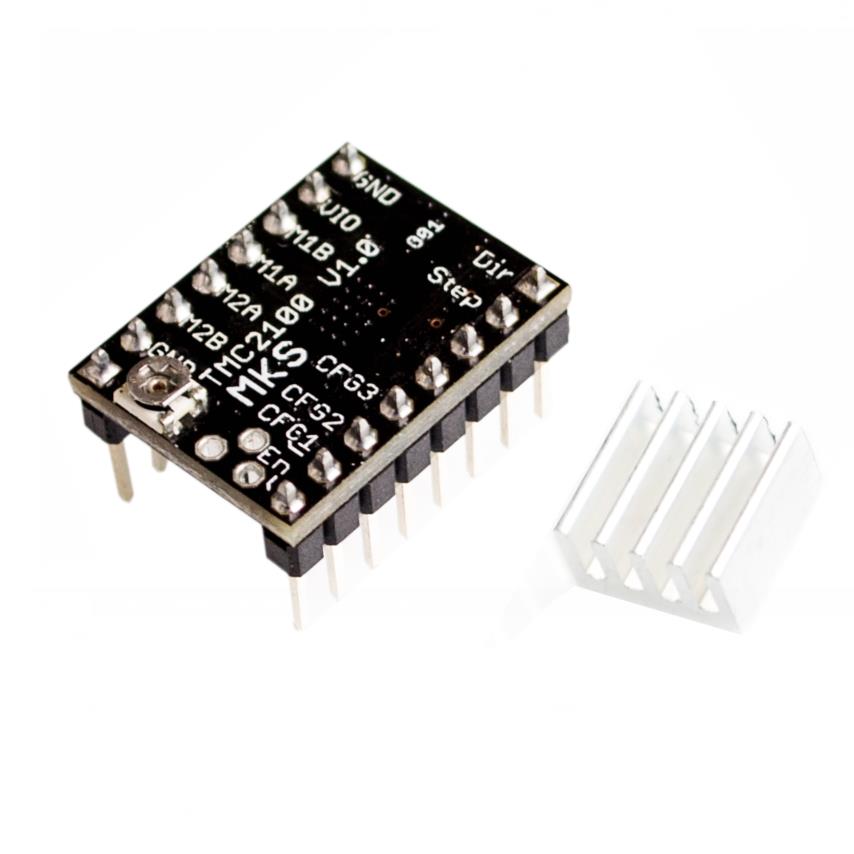
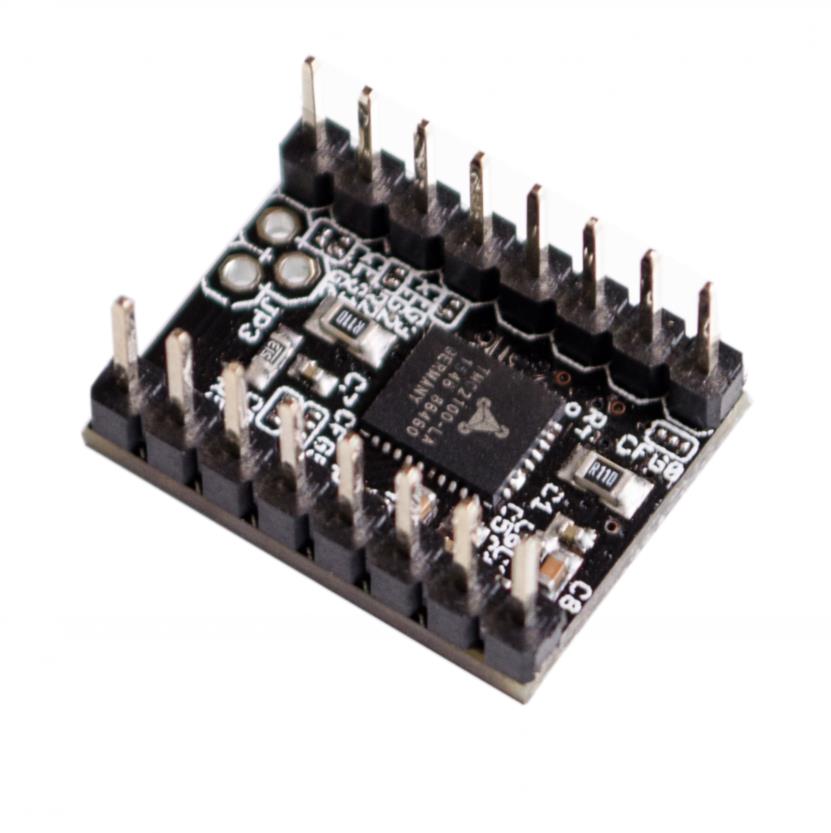